What is the inspection standard for glass bottles, and what standard is the index certificate for glass bottles based on? It is roughly divided into five steps, which are listed below for your reference and learning.
1, Deformation of the glass bottle
The glass drops into the forming mold, and the bottle is not well formed. At this time, if the temperature of the glass liquid is too high, the bottle will often be deformed. This can also happen if the top of the bottle is too heavy. If the bottom of the bottle cools slowly, the high temperature will also soften the bottom of the glass bottle, and there will be traces of the conveyor belt on the bottom of the spirit bottle, which will cause the bottom of the bottle to be uneven. Therefore, the initial design of the glass bottle is very important, not only the appearance is fashionable, but the structure of the design should also conform to the current industrial level.

2, The glass bottle body material traces
The most common thing in glass bottle factories is material marks, which are very common in the production process of glass bottles. Some material marks are very large and very conspicuous, while others are very thin and need to be seen in reflected light. This phenomenon often occurs at the mouth and body of the bottle, and occasionally at the shoulder and neck of the bottle. The reason for this is that the temperature of the furnace is too low. There are two ways for our company to rule out this situation. The first is to hire an experienced engineer, and the engineer can judge what temperature should be used for what bottle type based on rich experience. The second is to add a QC in every link of production. At the same time of machine inspection, manual inspection is added, and it is every link, which will greatly improve the quality of products and save production time.
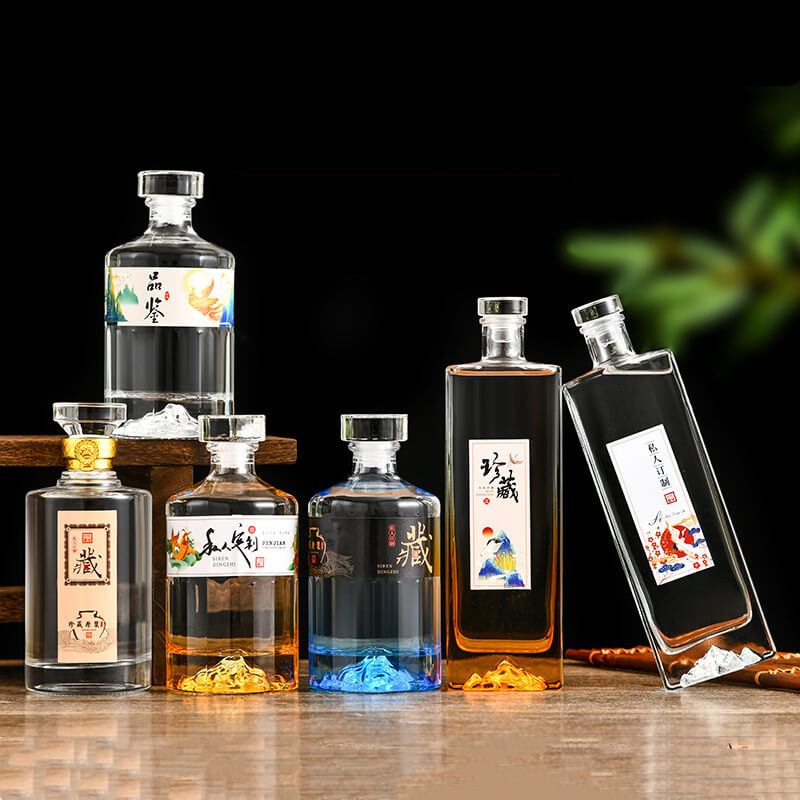
3, The thickness of the glass bottle is uneven
This situation is also a common phenomenon of glass bottle quality problems. The reason for this problem is that when the glass bottle manufacturer processes the glass gob, the glass gob is not heated uniformly, so the temperature is not uniform, which will lead to this problem in the glass bottle. The part with high temperature has strong fluidity, low viscosity and is easy to blow thin; the part with low temperature has poor fluidity, high viscosity and thicker. In addition, a similar situation occurs when the mold is not heated uniformly. On the side with high mold temperature, the glass cools slowly and is easy to blow thin; on the side with low temperature, the glass cools quickly, so it will be thicker. Our solution to this problem is still to use professional engineers and decades of industry experience to prevent such problems from happening.

4, The glass bottle crack environment
There are all kinds of cracks on the glass bottle, some are creases, and some are very fine wrinkles. The main reason for this is that the drop temperature of the glass bottle is too low, the drop is too long, and the drop is low. It is caused by deviation from the center of the initial mold, thereby sticking to the inside of the mold cavity.

5, Bubbles
The most troublesome thing for glass bottle manufacturers is the problem of bubbles. In the production process, the air bubbles are often several large air bubbles or a group of small air bubbles. This problem is related to the raw materials. We have long-term and reliable raw material suppliers, and set up professional QC in each link of production. Once similar problems are found, they will be rectified immediately from the source. It not only improves the quality of the product, but also greatly improves the production speed of the product and saves the production cost.