5. Bottle bottom defect
Bottle bottom crack: shallow crack at the bottom of the bottle.
Bottom explosion: deep cracks in any direction at the bottom of the bottle, most of which are radial.
Concave bottom: The center of the bottle bottom is abnormally concave.
Convex bottom: the center of the bottom of the bottle protrudes outward, and the bottle is placed on the flat plate, swinging unevenly.
The bottle bottom is uneven: it is unstable to stand on the plane due to the deformation of the bottle bottom. The swing is uneven.
Mold bottom damage: the glass at this part of the bottle bottom is convex due to the damage of the bottom mold.
Mold bottom line: the glass penetrates into the joint between the molding mold and the bottom mold or forms a burr due to poor matching of the mold bottom.
The bulkhead line is not straight: the bulkhead line is not in the center of the bottle bottom, and it deviates to one side.
Inclined bottom: the inside of the bottle bottom is inclined, but the inclination exceeds the specified requirements. Generally, the proportion of bottom deviation is controlled by 1:2mm.
Thin bottom: the bottom glass is not enough to meet the thickness required by the design, and the bottom deviation sometimes leads to a thin bottom.
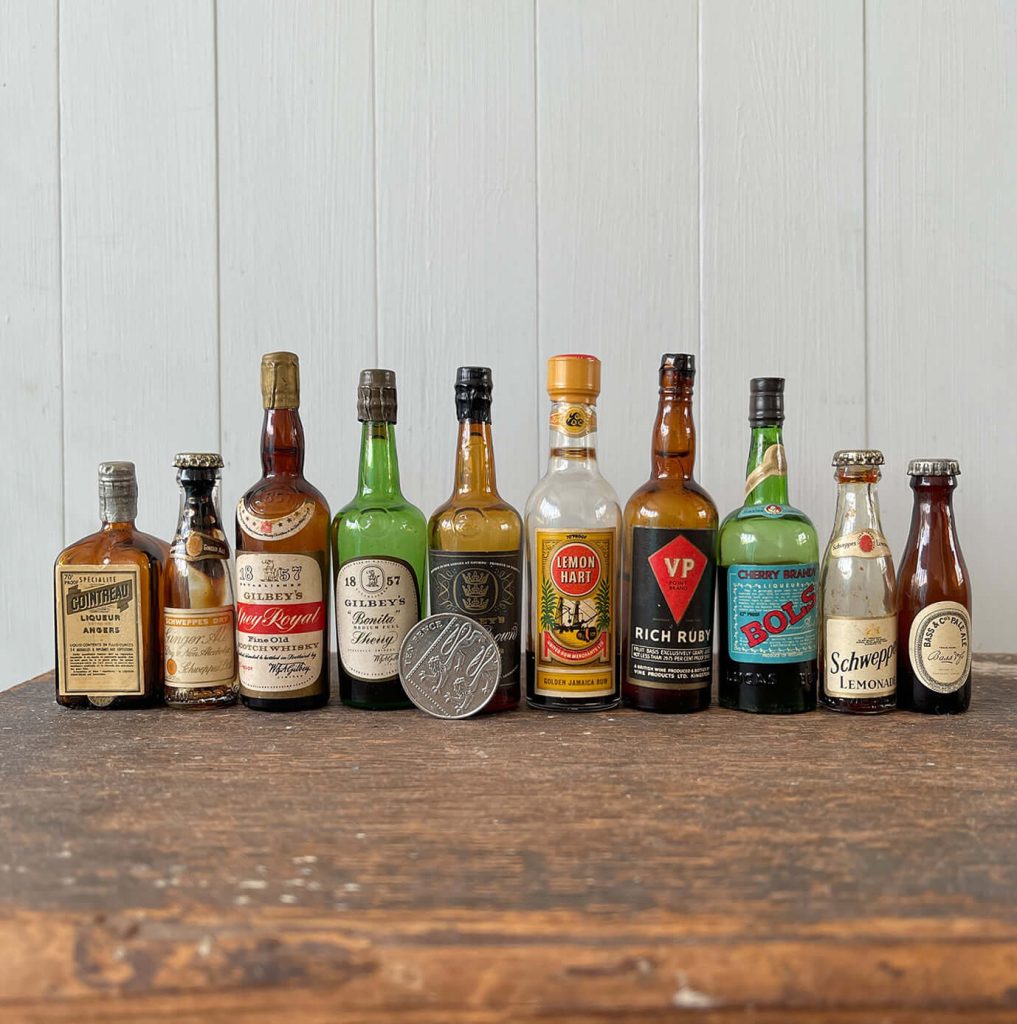
6. Seam defect
Seam crack (burst seam): a vertical crack at the seam of the forming die. Its shape is different from that of hot die crack.
Poor stitching of the initial mold: the iron bowl line of the bottle body is convex and sharp. After forming, the initial mold line is depressed.
Rough edge of forming mold seam: bulge at the forming mold seam, which is opposite to the shape of the initial mold seam.
Forming staggered seam: the two halves of the forming die are not well matched, and the seam line is stepped. One high and one low.
Bulkhead thread is too deep: the glass enters the parison mold and forms obvious zigzag seam at the bulkhead pull seam. Visual inspection shows obvious depression of bulkhead line
Bulkhead burr (rotten bulkhead line): the bulging and serrated bulkhead line is formed at the fitting of the bulkhead and the iron bowl.
Rough edge of bottle mouth/parison molding seam: the joint between the mouth and the iron bowl is not smooth to form a convex, stepped or serrated seam.

7. Measurement defect
The bottle body is too large: the diameter of the bottle body exceeds the upper limit of the standard. When the bottle body is depressed, it may also cause the body diameter to be too large at some point.
Bottleneck blockage (narrow neck): the inner diameter of the bottleneck is less than the specified requirements. Some products indicate the effective length of the inner plug on the design drawing according to the customer’s filling pipe requirements. If there is a narrow neck, it is unacceptable. Products with no special requirements shall be judged by visual inspection.
Bottleneck inner ring: the glass concentric ring at the neck or upper part of the bottle body.
The inner diameter of the bottle mouth is too small: the inner diameter of the bottle mouth is less than the specified requirements. It can be measured with plug gauge or vernier caliper. The inner double port may cause the inner diameter of the port to be too small.
Super high: the bottle height exceeds the upper limit of the standard, and the bottle height may also exceed the standard due to the elongated bottleneck.
Bottle height: the bottle height cannot reach the lower limit of the standard, and the bottle shrinkage is too large or the bottom of the seat will cause the bottle height to be low.
The bottle body is not round: ovality is a deformation of the bottle body section from round to oval, which is usually expressed by the difference between the long and short axes of the ellipse.
That is, the difference between the large value and the small value of the same initial measuring surface after one revolution exceeds the standard range of out-of-roundness of the bottle body.
Bulging of the bottle body: the bottle body is deformed and protrudes outward beyond the specified requirements.