Occasionally, glass bottles may experience issues with a narrow internal diameter at the neck (also known as a “fine neck” or “small opening”). This can occur in two forms: the entire opening narrows uniformly, or only part of it does. This problem can be assessed using a standard iron rod or a plug, which may encounter resistance or not fit at all. The causes for these issues typically relate to three factors: feeder machine material shape and temperature, core design and operation, and production practices. Below, each factor is analyzed:
1. Feeder Machine Material Shape and Temperature
- Causes: If the droplet shape at the top is excessively pointed or narrow, or if the droplet temperature is inconsistent or too high, it can lead to a narrow opening in the glass bottle.
- Solutions: Adjust the droplet shape to reach an optimal size. Use a pipe feeder to cool the droplets to an appropriate temperature. Additionally, if the core design is not well-conceived, it can contribute to a fine neck. If the oil residue is excessive or if the glass material is in contact with the core for too long or too short, it can result in lower core temperatures, leading to a narrow opening.

2. Core Design and Operation
- Preventive Measures: Operators should regularly inspect for excessive oil residue and clean it immediately upon detection. If the bottle clamp is not used correctly, it may cause the neck to be pinched, resulting in a narrower opening. It is crucial to measure the specifications of the bottle neck carefully and select the appropriate clamp before operation.
3. Production Practices
- Additional Issues: Improper use of initial mold cooling air or incorrect distances between the blowing inspection head and the bottle neck can also contribute to narrowing issues. Operators should ensure they are following proper heating and inspection protocols to address these problems proactively.
Consequences of Narrow Openings
- A narrow opening can lead to difficulties during filling, as the filling tube may not fit inside the bottle neck. If the cap includes a plug, discrepancies between the plug and the bottle neck diameter may occur, potentially causing the plug to be pushed out during capping. This can result in leaks or fluid seeping out of the bottle.
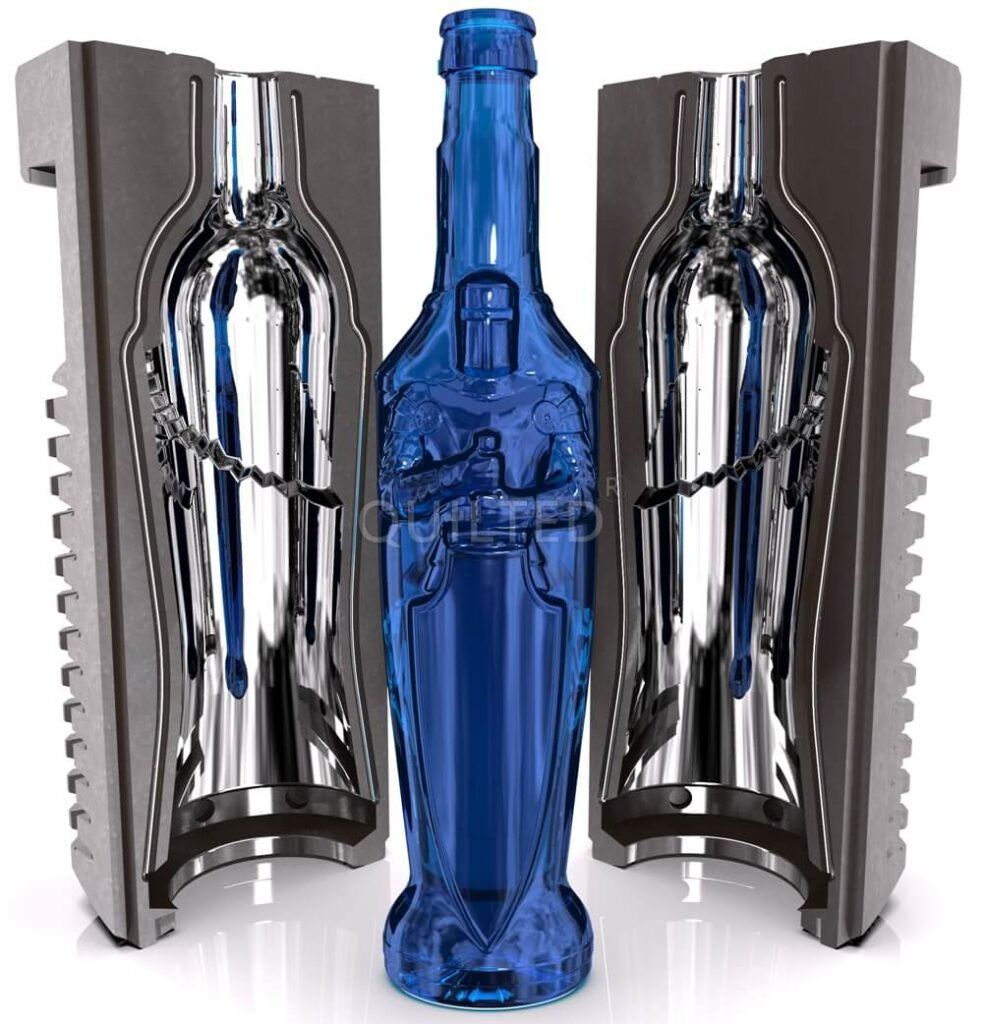
Conclusion
Addressing narrow openings in glass bottles requires careful attention to the feeder machine settings, core design, and operational practices. By implementing thorough inspections and adjustments, manufacturers can minimize defects and ensure efficient filling processes, ultimately maintaining product quality and safety.